În condițiile dezvoltării dinamice a proceselor din economia modernă, crearea unor proceduri de producție și control din ce în ce mai complexe, una dintre cele mai relevante abordări ale îmbunătățirii acestora este introducerea unor metode de optimizare a diverselor pierderi. În primul rând, aceasta se referă la resursele întreprinderilor - temporare, financiare, tehnologice, energetice și altele.
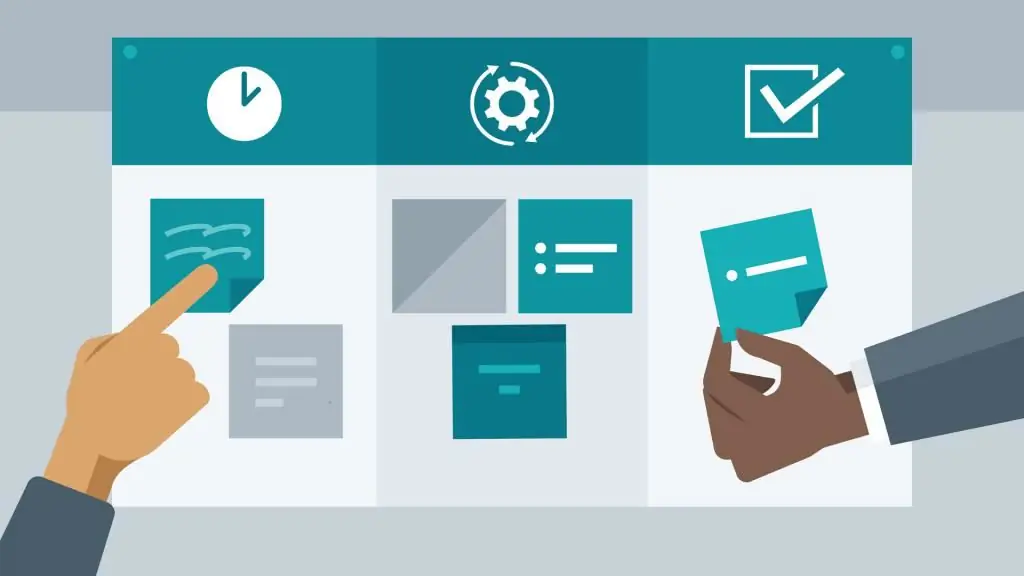
Caracteristici ale activității
În practică, există un anumit plafon, care este asociat cu nivelul de dezvoltare tehnologică și organizatorică a sistemului (organizație, întreprindere). Este clar că este nepotrivit să ceri automatizarea totală a producției de la un mic atelier de croitorie după diverse criterii și, mai ales, economice. Oricum, indiferent de dimensiunea sistemului, este necesar să se asigure utilizarea maximă și optimă a resurselor disponibile cu pierderi minime, ceea ce este valabil pentru orice organizație și activitate.
În acest caz, devine necesar să se utilizeze tehnici progresive de management al proceselor care se bazează pe teoria creării producției lean sau „lean”. Acestea includ sisteme 5S și TPM, maparea fluxului de valoare și SMED etc.
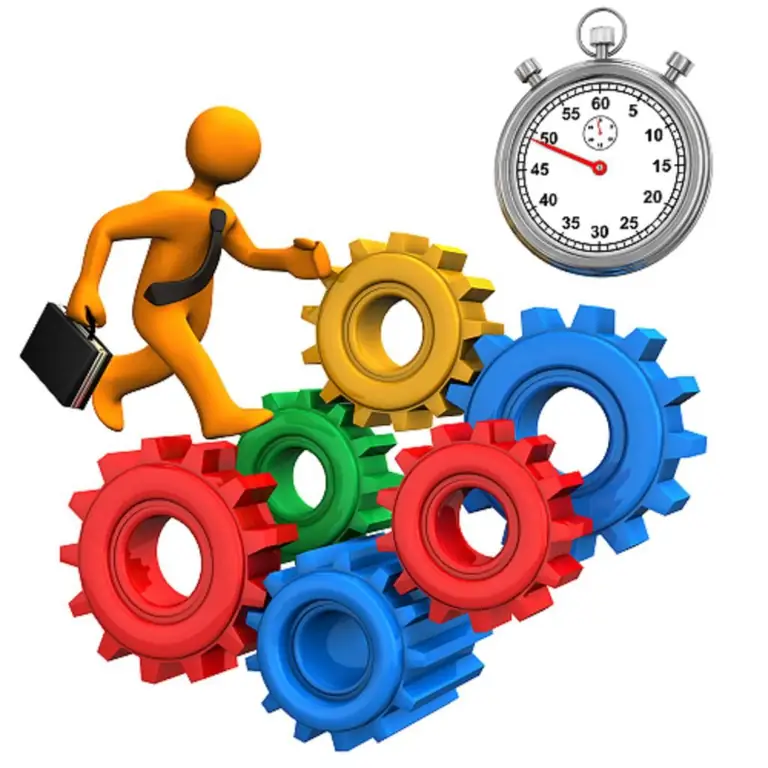
Scopul inovației
Producția lean („lean”) este un sistem de abordări speciale ale organizării activităților, care are ca scop principal eliminarea diferitelor pierderi din sistem. Mecanismul este destul de simplu: tot ceea ce nu adaugă valoare clientului trebuie clasificat ca redundant (deșeuri) și eliminat din sistem. Este clar că conceptul de „pierderi” este piatra de temelie, deoarece definiția lor va afecta în mod direct eficacitatea metodei. În acest caz, a învăța să mapați fluxul de valoare al specialiștilor dvs. este un avantaj semnificativ pe piața de livrare a serviciilor
Tipuri de pierderi
„Lean manufacturing” este unul dintre conceptele fundamentale ale logisticii producției. Și, deși există mai multe abordări diferite pentru a determina pierderile, vom evidenția cele mai universale tipuri:
- Timp de așteptare - orice timp de întrerupere în activități reduce valoarea produsului final. Așteptarea materialelor, a reparațiilor echipamentelor, a informațiilor sau a instrucțiunilor de la conducere încetinește procesul și crește costul implementării acestuia.
- Operațiuni inutile (prelucrarea inutilă a produselor) - operațiuni tehnologice inutile, etapele proiectului, tot ceea cefurnizate prin proceduri standard, dar pot fi nivelate fără pierderea încrederii clienților.
- Mișcări inutile ale lucrătorilor - căutarea de unelte, echipamente, mișcări iraționale din cauza organizării proaste a locului de muncă etc.
- Mișcarea inutilă a materialelor - proasta organizare a sistemului de inventariere, lipsa logisticii de transport progresive și a mecanismelor de externalizare a logisticii.
- Exces de inventar - blocarea capitalului de lucru al unei organizații ca urmare a cheltuielilor mari pentru articolele din stoc în exces.
- Deșeuri tehnologice - sisteme de prelucrare a datelor, procese tehnologice și rute de procesare învechite.
- Pierderi prin supraproducție - producția unei cantități în exces de produse, ceea ce duce la creșterea costului depozitării, transportului și vânzării ulterioare a acestuia.
- Pierderi intelectuale - lipsa mecanismelor de încurajare a inițiativei lucrătorilor și angajaților, un sistem slab de propuneri de raționalizare, suprimarea unei abordări creative a muncii.
Una dintre cele mai comune metode de eliminare a risipei de sistem și de eficientizare a execuției proiectelor este maparea fluxului de valoare. Lean manufacturing vă permite în același timp să creați un sistem adaptiv care răspunde flexibil la schimbările din mediu.
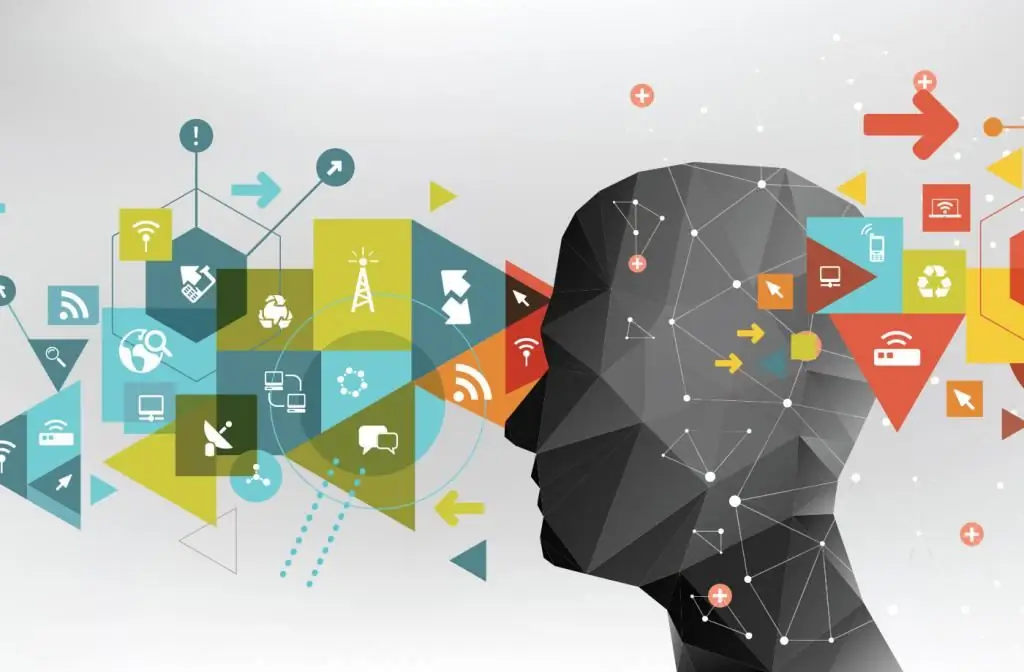
Flux de valori
Fluxul de valoare este un set de toate acțiunile (operațiunile) care sunt efectuate asupra unui produs pentru a realizastarea cerută sau obţinerea caracteristicilor cerute. Acțiunile sunt diferențiate în două grupuri:
- crearea valorii produsului (valoare adăugată);
- nu adaugă valoare produsului.
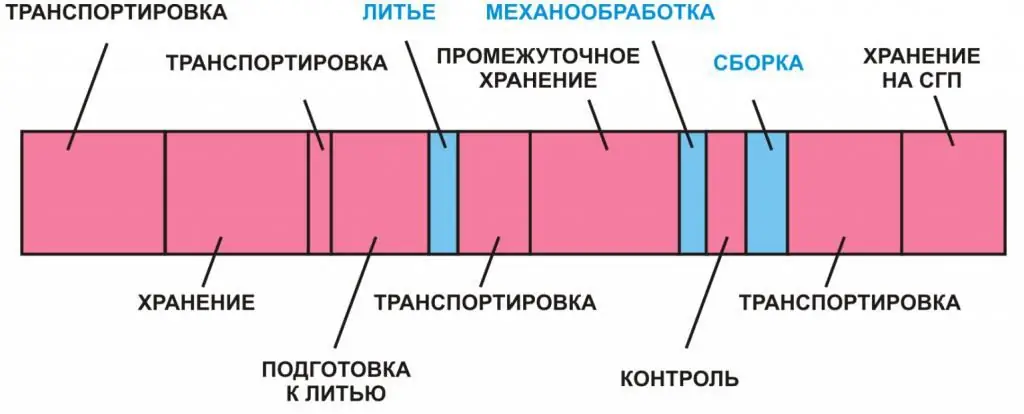
După cum se poate observa din figura prezentată, etapele de schimbare tehnologică a produsului (culoare albastră) adaugă valoare produsului, iar etapele operațiunilor auxiliare - pregătire, transport, depozitare - (culoare roz) - dimpotrivă, reduceți mai degrabă valoarea produsului din cauza pierderilor inutile de timp.
Proces de cartografiere
Baza tehnicii de cartografiere este dezvoltarea unui algoritm grafic special care arată procesul de creare a produselor (implementarea proiectului) în timp. Acest algoritm se numește o hartă a fluxului de valori, care este un model grafic bazat pe un anumit set de simboluri (semne, simboluri).
Principalele avantaje ale cardului:
- obținerea unui model grafic al procesului în desfășurare, luând în considerare diverse procese suplimentare pentru o percepție vizuală holistică (sarcina este de a vedea fluxul general al evenimentelor);
- abilitatea de a detecta diferite tipuri de pierderi în toate etapele proiectului;
- posibilitate de optimizare parametrică a modelului rezultat pentru a minimiza costurile de tot felul;
- lucrează cu diverși indicatori ai algoritmului, care se vor reflecta în îmbunătățirea proceselor reale.
Formarea mapării fluxului de valoare pe baza graficelor standard șisimboluri - blocuri dreptunghiulare și triunghiulare, săgeți direcționale și în trepte și alte figuri. Face posibilă înregistrarea etapelor procesului studiat într-o singură limbă pentru toți specialiștii. În același timp, se recomandă diferențierea simbolurilor în funcție de fluxul considerat - material sau informațional.
Lean Value Stream Mapping vă permite să identificați toate locurile în care se acumulează articole inutile.
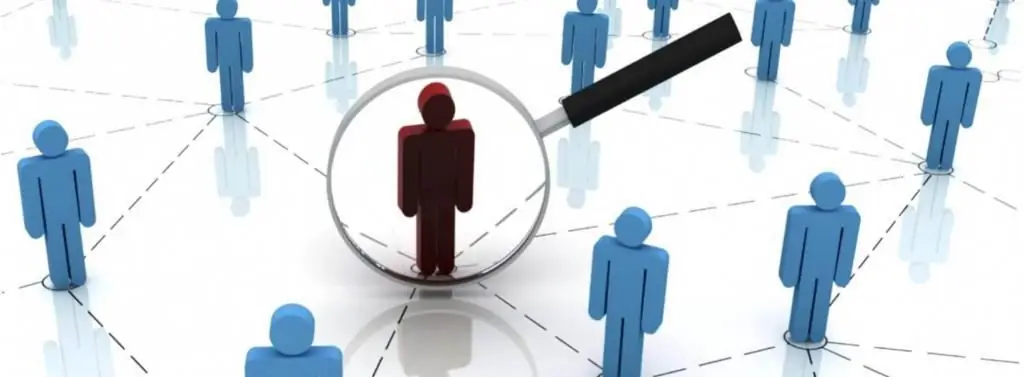
Reguli de construcție
Cartografierea fluxului de valoare implică o serie de pași simpli care vor crea rapid modelul de proiect necesar cu parametrii dați. De exemplu:
- Efectuați o analiză a fluxurilor de materiale și informații pentru a obține o imagine fiabilă a stării curente a procesului.
- Parcurgeți fluxurile în direcția înainte și înapoi pentru a identifica cauzele ascunse ale pierderilor și pentru a găsi modele negative.
- În orice circumstanțe, luați singur măsurători de timp, fără a vă baza pe rezultatele altor specialiști sau pe valorile standard.
- Dacă este posibil, creați o hartă și pe cont propriu, ceea ce va face posibil să evitați atât greșelile altora, cât și soluțiile șablonului.
- Concentrați-vă pe produsul în sine, nu pe acțiunile operatorilor sau ale echipamentelor.
- Construiți o hartă manual, folosind un creion sau markere.
- Vizualizați elementele unui proces folosind culori pentru a îmbunătăți percepția.
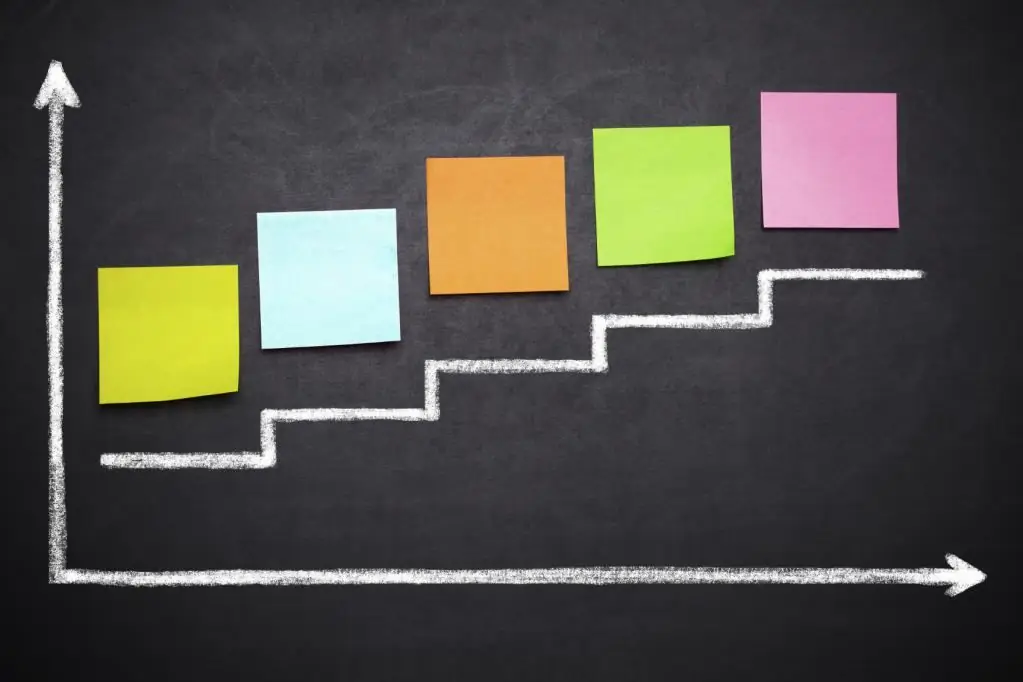
Exemple de mapare a fluxului de valoare
Să luăm în considerare un exemplu de creare a unei hărți de flux în domeniul managementului documentelor, inerente activităților oricărei instituții.
Sarcina principală este de a alege cel mai bun furnizor. Procesul standard de decizie este următorul: selecția unui furnizor (12 zile) - executarea textului contractului (3 zile) - coordonarea în servicii funcționale (18 zile) - viza de persoană autorizată (3 zile) - obținerea sigiliul capului (1 zi) - obținerea semnăturii contrapărții (7 zile) - înregistrarea în autorități (3 zile).
Total primim timpul necesar pentru a obține contractul necesar - 48 de zile. Rezultatul analizei a fost descoperirea blocajelor schemei decizionale.
Modificări principale după analiza hărții:
- S-a emis ordin de delegare a semnăturii unei părți din documente șefilor de departament (reducerea sarcinii asupra aparatului administrativ și reducerea semnificativă a numărului de avize).
- Au fost dezvoltate aceleași cerințe pentru toate serviciile (o înțelegere comună a cerințelor pentru documentele contractuale, o scădere a numărului de erori ale executanților).
- Principiul end-to-end al analizei documentației a fost implementat prin crearea unui grup comun de specialiști din diferite servicii.
- S-au folosit noi șabloane de contract.
- Mecanismele de procesare a documentației prin intermediul sistemului electronic au fost optimizate.
- A fost dezvoltat un sistem electronic de urmărire a calității documentelor care trec prin etapele procesului.
Rezultat principalcartografierea fluxului valoric a devenit o reducere de două ori a timpului pentru obținerea documentației contractuale, inclusiv a timpului pentru aprobare în serviciile departamentale.
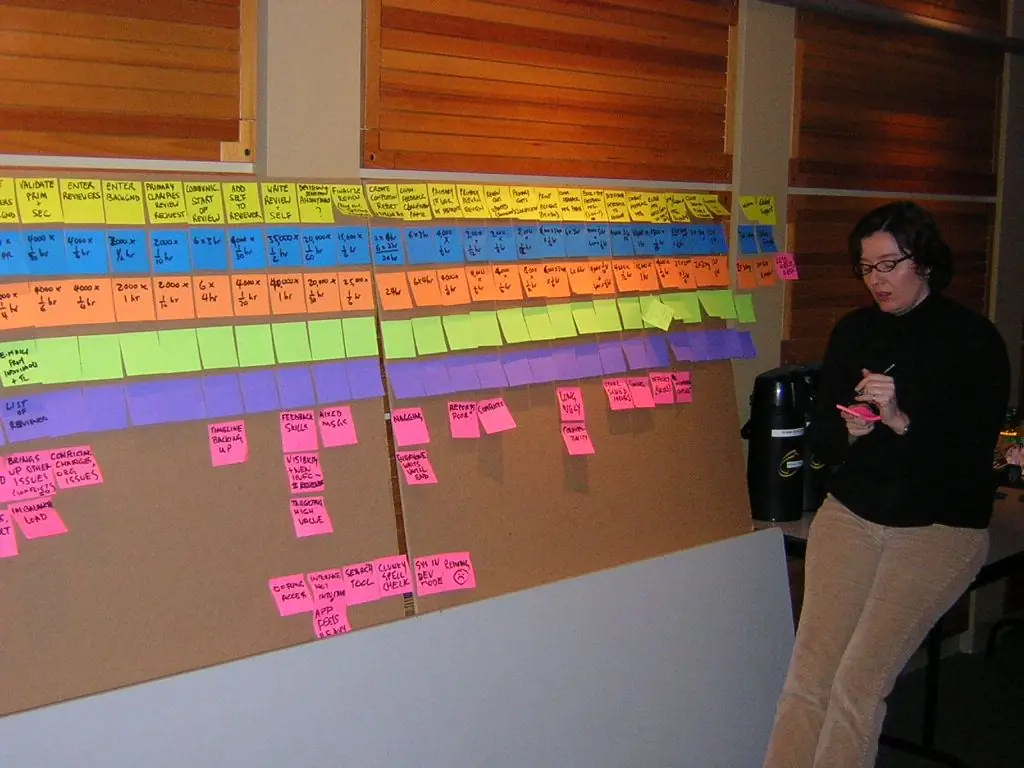
Concluzie
Recent, maparea fluxului de valoare (VSM, Value Stream Mapping) a devenit o metodă foarte comună de optimizare a activității diferitelor organizații. Acest lucru se datorează simplității și accesibilității sale, costuri minime cu efect benefic acumulându-se în timp. Există multe exemple de implementare cu succes a acestei metodologii de logistică de producție de bază: întreprinderile Rostec Corporation, Transmashholding, Căile Ferate Ruse etc. Recent, a fost creat un sistem de manufacturing lean la nivel federal în instituțiile medicale. În special, se propune să se efectueze cartografierea fluxului de valoare în policlinici.
După cum puteți vedea, întregul potențial al metodei luate în considerare abia începe să fie dezvăluit.